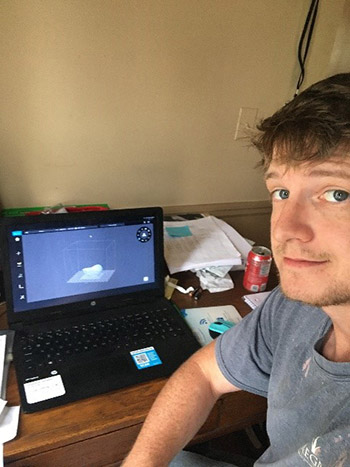
Valdosta, GA – Students William Hoover, Shawn Lucas, and Tyler Hall started the spring semester back in January at Wiregrass Georgia Technical College, excited to be completing their last course before earning their associate’s degree. Enrolled in mechatronics and engineering, the three students started working on their capstone project, a semester-long, collaborative effort to design and manufacture a product using real world engineering practices and the same cutting-edge technologies found in local manufacturing facilities.
By mid-March and the students were nearly complete. After conducting research and design, cost analyses, prototyping, and time studies, the students were preparing to present their capstone project to a panel of industry experts. Then the word came that due to COVID-19, colleges within the state would be transitioning to 100% online education for the remainder of the semester. With so many technological capabilities such as video-conferencing and other online platforms, the students could easily present their work and complete their capstone project. However, William, Shawn, and Tyler recognized an opportunity to do more.
Using Industry 4.0 technologies such as digital manufacturing, 3D printing, and real-world collaborative design software, the students decided to cease work on their nearly complete capstone project and instead use the opportunity to join the battle against the spread of the COVID-19 outbreak.
William, Shawn, and Tyler collaborated with their Wiregrass instructors, Joshua Whittington and Joe Sumner, to design and 3D print respiratory masks. The team conducted several test runs, with each student handling different aspects of the design, cost analysis, and materials needed for a limited mass production run.
William Hoover, who actually purchased his own 3D printer, was able to conduct test prints at his home, and share the files with his teammates and instructors. Hoover, who has a Bachelor of Science in chemistry, says he finds the hands-on aspect of the project exciting.
“When the college shifted to 100% online, I knew that I would miss the face to face interaction with my peers and instructors,” said Hoover. “However, being able to use 3D printing technology to create something that will benefit my fellow students and instructors when the school reopens is exciting.” The college is working toward returning students to lab work in a limited capacity and the masks will be utilized to provide a safe and healthy environment.
With instructors Joshua Whittington and Joe Sumner operating the 3D printers at the college, and the students monitoring the machines remotely online, the group have been able to successfully manufacture as many as 10 respiratory masks every 24 hours. The masks are manufactured from a hard-shell ABS plastic, and require a reusable filter. William, Shawn, and Tyler are conducting a cost analysis to determine the possibility of providing masks on a broader scale if the current situation continues.
For Tyler Hall, the chance to be a part of this project was even more personal. As a cancer survivor, the 26-year-old engineering student knows firsthand the significant role that rapid response, manufacturing, and technical education can play in the healthcare sector, and is eager to be a part of the project.
“I’m just glad to be a part of something so positive here, said Hall. “Even if it seems like a small role to play, I’m personally excited to use my skills and personal experience as a motivation to be a part of something so big during this time.”
For the instructors, seeing the students so eager to work on a meaningful and impactful project has been encouraging.
“The skills the students have learned, and are now putting to use, are relevant across multiple fields, including mechatronics, engineering, healthcare, and project management,” said Joshua Whittington, Wiregrass Engineering and Mechatronics Instructor.
“To see our mechatronics and engineering students take ownership of this project, and leverage the capabilities of Industry 4.0 in an effort to contribute to such a worthy cause is heart-warming and meaningful,” said Joe Sumner, Wiregrass Associate Vice President of Program Development. “The reality is, manufacturing and design no longer happen in a single building. Various stages of the process occur all over the globe, and the skills our students are utilizing in this project are fully preparing them for employment in today’s manufacturing and engineering sectors.”
With the multitude of online technologies, Wiregrass Georgia Technical College students have been able to continue their training and learning remotely, even under such unprecedented circumstances. Dr. Tina Anderson, president of Wiregrass Georgia Technical College, expressed pride in the students’ ability to apply their skills in new and innovative ways.
“Our students participate in real-world design and manufacture processes in the mechatronics program. We are very proud of their ability to take classroom lessons and apply them to healthcare needs in the midst of the COVID-19 pandemic.”
If you are interested in supporting the students’ effort to make masks, Wiregrass is accepting donations to pay for the materials needed to manufacture the masks. Anyone interested in making a donation may contact Crissy Staley with the Wiregrass Foundation at Crissy.staley@wiregrass.edu or 229-333-2124. For those interested in learning more about essential careers in Mechatronics and Engineering, visit www.wiregrass.edu to learn more. The college will be hosting a second Free Application Week April 27- May 1. Please see special notices on the college’s website regarding new summer semester admission requirements due to COVID-19. The college is open by virtual methods while students finish spring semester online.